PSA Nitrogen Generation Plant
A PSA (Pressure Swing Adsorption) Nitrogen Generation Plant is a complicated commercial device designed to provide excessive-purity nitrogen gasoline by way of utilizing the precept of adsorption.
Nitrogen is an inert fuel extensively utilized in numerous industries, inclusive of chemical production, electronics, food and beverage, pharmaceuticals, and metallic processing. The PSA procedure is a cost-powerful and energy-efficient approach for generating nitrogen on-web site.
Principle of Operation:
Adsorption and Desorption:
The PSA process is based on the capacity of positive materials, known as adsorbents (commonly carbon molecular sieve or zeolite), to selectively adsorb nitrogen molecules from a feed gas mixture.
The method entails alternating tiers: adsorption and desorption.
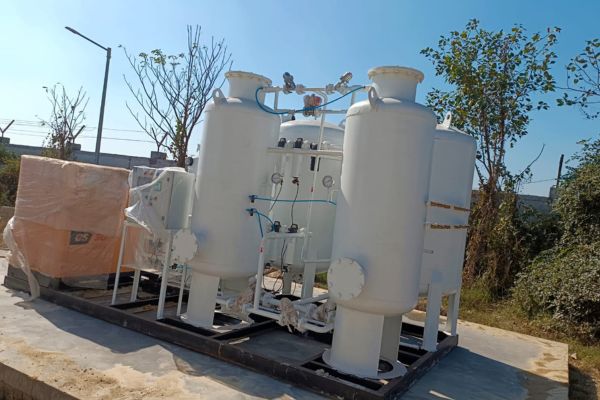
Adsorption Stage:
Feed air (composed of oxygen and nitrogen) is compressed and introduced into a vessel containing the adsorbent material.
The adsorbent preferentially captures oxygen molecules, permitting the nitrogen to skip through and be accrued because the product fuel.
Desorption Stage:
The strain within the vessel is decreased, causing the adsorbent to launch the captured oxygen molecules.
The launched oxygen is then vented, and the adsorbent is ready for the subsequent cycle.
Dual Vessel Configuration:
PSA nitrogen generation flora frequently encompass vessels to make certain a continuous supply of nitrogen.
While one vessel is in the adsorption section, the opposite is within the desorption section.
Components of a PSA Nitrogen Generation Plant:
Air Compressor:
Compresses ambient air to the specified stress for the PSA process.
Air Treatment System:
Removes impurities (together with moisture, oil, and dirt) from the compressed air to protect the adsorbent fabric.
PSA Vessels:
Typically two vessels filled with an adsorbent material like carbon molecular sieve.
Valves and Piping:
Controls the flow of gases among different ranges of the procedure.
Nitrogen Receiver Tank:
Stores the generated nitrogen for distribution to various applications.
Control System:
Monitors and controls the entire PSA nitrogen era procedure, making sure premiere performance and protection.
Advantages of PSA Nitrogen Generation:
On-Site Production:
Eliminates the want for garage and transportation of nitrogen gas, decreasing logistical complexities.
Cost-Effective:
Lower operational fees compared to conventional nitrogen supply methods, including liquid nitrogen or nitrogen cylinders.
Energy Efficiency:
The PSA system is power-efficient, in particular when as compared to cryogenic separation strategies.
High-Purity Nitrogen:
Capable of manufacturing nitrogen with purity stages starting from 95% to ninety nine.999%, relying on the application.
Customization:
Systems can be designed to meet particular flow fee and purity requirements of various industries.
Applications:
Chemical and Petrochemical Industry:
Blanketing and purging processes, stopping oxidation and making sure safety.
Food and Beverage Industry:
Modified atmosphere packaging, stopping spoilage and increasing shelf existence.
Electronics Industry:
Soldering, wave soldering, and reflow tactics wherein nitrogen prevents oxidation.
Pharmaceutical Industry:
Inerting and blanketing at some stage in drug manufacturing to maintain product high-quality.
Metallurgical Processes:
Heat-treating and annealing operations wherein nitrogen prevents oxidation of metals.
Oil and Gas Industry:
Pipeline protection and inerting for safety in the course of protection operations.
Considerations and Maintenance:
Adsorbent Replacement:
Over time, the adsorbent material might also lose its effectiveness and require replacement.
Regular Maintenance:
Routine checks of valves, filters, and other components are necessary to ensure regular performance.
Safety Measures:
Proper protection protocols ought to be in location, particularly throughout the desorption phase, because it entails the discharge of oxygen.
Monitoring and Control:
Continuous monitoring of the device parameters is critical for most advantageous overall performance and efficiency.
Future Trends:
Smart Control Systems:
Integration of advanced control structures with IoT skills for far off monitoring and predictive preservation.
Green Technologies:
Exploration of eco-friendly adsorbents and energy-green methods for a extra sustainable operation.
Industry four.Zero Integration:
Integration with Industry 4.0 concepts for enhanced automation and information analytics.
In end, PSA Nitrogen Generation Plants play a critical position in presenting a reliable and on-site supply of excessive-purity nitrogen for a extensive variety of industrial applications. As technology continues to strengthen, these systems are likely to become extra green, price-powerful, and environmentally pleasant, assembly the evolving desires of diverse industries.